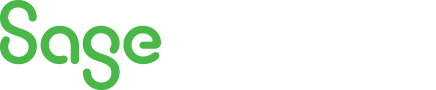
Sage 100 Newsletter – Q3 2022
Keeping You Up-To-Date With Information About Sage 100
Common Problems Facing Warehouse Management
A warehouse is a complex business environment where a number of different tasks and processes must all fit together to create a seamless and efficient workflow. The advent of the always-on customer that expects fast turn around times and end-to-end visibility means that warehouses must have the systems in place to produce these results. Distribution cannot be slow and riddled with mistakes for any company that wants to remain competitive in the modern world. Managing this workflow so that the warehouse can gain these competitive advantages can present several key challenges, such as:
Increasing Transparency:
A modern warehouse needs a clear view of across all business functions, with centralised, real-time data. If you don’t have an accurate and clear view of stock levels and movement, it is more difficult to communicate clearly with customers around stock availability, follow FIFO principles, or manage seasonal demands.
Transparency within your processes is also essential for meeting regulatory requirements or managing cold-chain continuity, by giving to an end-to-end view of the movement of your stock. By enabling transparency across the supply chain it is also easier to eliminate counterfeit products, manage regulated products such as tobacco, and report on environmental impact and sustainability goals.
Optimising Labour:
As warehouse technology and systems become more complex, and retail increasingly shifts to ecommerce, the demand for warehouse labour across various skills levels will continue to increase.
Labour costs are generally one of the highest line items on any business budget. This means that labour-intensive processes, or workers that are not performing optimally will cost the company money. Not only must employees have the skills and training needed to easily complete the tasks required of them, but the entire warehouse process should be set up to optimise the workflow.
Workers that receive clear tasks, broken down into simple steps, to create streamlined processes can work more effectively. In addition to this, solutions such as eliminating manual paperwork and optimising walk-paths while picking, can reduce the time it takes to complete certain tasks. Fewer staff, working more effectively can get more done, faster and more accurately with the right processes and equipment in place.
Meeting Customer Expectations:
Customers are expecting an increasingly fast turnaround when ordering products. Moreover, they want to be able to track their order and get up-to-date and accurate information on its status.
To meet these growing customer expectations warehouses must enable fast and accurate picking, with a clear view of where all items are in the process. Accurate picking is also essential to avoid returns, complaints, and duplicate work, which not only decreases customer satisfaction but also costs the company time and money.
Stock visibility ensures better communication with customers upfront around what items are available and in stock, or what the lead time will be. This helps to manage the customer’s expectations and lets them avoid disappointment.
An easy and streamlined reverse logistics process is also essential. Consumers are more comfortable with returning products that do not suit their needs, and they want the process to be as simple as possible. In the warehouse, being able to assess the reason for the return and escalate it accordingly or get the item back into the inventory when appropriate will also lower costs and ensure stock integrity.
Facing the Challenges: GraniteWMS
These are all problems that can prevent a warehouse form operating at its full potential. As the pace of technological innovation continues to accelerate, it is no longer feasible for warehouses to keep doing things as they did in the past.
The Granite Warehouse Management System is a simple and lightweight application that will help you address these common warehouse challenges. With a focus on barcode scanning at every point of interaction, GraniteWMS gives you a clear end-to-end view of every item and transaction in your warehouse.
The system is easy to use and provides simple step-by-step instructions to users for all processes, enabling workers to optimise output and eliminate picking errors. With a data and analytics dashboard that gives an accurate, live view of stock levels and transaction progress, it is possible to clearly communicate with clients around order availability and status.
GraniteWMS is a lightweight system designed for the mid-market warehouse need. It is not bloated with unnecessary functionality and can be implemented in your warehouse in weeks rather than months. Contact us today to find out how we can optimise your warehouse.
This article was originally published by GraniteWMS.