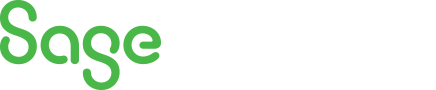
Sage 300 Newsletter – Q3 2021
Keeping You Up-To-Date With Information About Sage 300
Key KPIs to Track in Your Warehouse
Successfully managing a warehouse is all about performance optimization. If you can consistently manage the flow of stock through your warehouse so that products are delivered quickly and efficiently, with no mistakes, you will improve revenue and keep clients happy.
This is why it is essential to track the Key Performance Indicators (KPIs) within your warehouse. By tracking a few key aspects of your warehouse performance you will have a better understanding of where the inefficiencies are, how mistakes and are being made, and how they can be prevented.
The following are the top KPIs that every warehouse manager should be tracking:
1. Receiving Efficiency – To track receiving efficiency one must look at the time taken to process each receipt, the accuracy of the receiving, i.e. the proportion of the receipt correctly verified against the purchase order, and the volume of goods received by each employee, per hour.
By ensuring accuracy and efficiency in the receiving line of the warehouse it is possible to prevent mistakes and inefficiencies snowballing through subsequent processes down the line.
2. Put-away Optimization – Paying attention to optimal put-away of received goods means that every item has a designated location. This makes it easy to identify and find for convenient retrieval during the picking process. To optimize the put-away process consider the volume of stock put away per employee per hour. Also look at the percentage of items put away accurately at the designated location, and total time taken during the entire process of each put-away task.
If items are not being put away quickly enough, or accurately in their allocated locations this not only causes problems down the line, but could indicate other issues such as the need for additional labor or increased training.
3. Storage Utilization – A key element to consider in the warehouse is how effectively you are using the space you have available.
This includes the volume of inventory you are able to store per square foot, and what percentage of that space is regularly utilized. It also covers the carrying cost of inventory being held in stock. Factors such as insurance, service costs, and obsolescence all contribute to the cost of carrying excess stock.
The result is a delicate balance where warehouses must maximize storage utilization while reducing cost of inventory. It is important to have a brisk inventory turnover, and ensure a clear view of older stock, to reduce wastage.
4. Picking and Packing Speed and Accuracy – Being able to quickly and accurately pick and pack orders is essential to getting products out on time, reducing returns, and ensuring happy customers. To track the efficiency of the picking and packing process consider the percentage of orders picked and packed without error, the number of order lines picked per hour, and the overall time taken to pick each order.
It can also be important to look at the costs accrued by the process, including utilization of equipment during the process and the cost of packing materials and labels. This can uncover hidden inefficiencies and opportunities for optimization in the process.
5. Distribution Management – From the client’s point of view an order is not complete when it is dispatched, but when it arrives. Distribution has become an increasingly important part of warehouse management as clients increasingly expect fast turnaround of their orders.
It is important to monitor not only how long it takes an item to reach the customer and the number of orders that were delivered without error, but also how many back orders are there for items that are out of stock, and how many orders are accumulating waiting to be dispatched. These metrics can point to issues in planning and forecasting around stock holding.
6. Return Rates – Finally it is essential to track and manage returned items coming back into the warehouse. This includes not only optimizing the process of receiving and processing retuned goods, but also analyzing return rates, and identifying the major causes.
By separating returns according to the reason for the return it is possible to track down the points in the process where mistakes are occurring and fix them. This will reduce costs, improve processes and lead to better customer satisfaction.
Come talk to Net at Work about putting the right technology in place to track these KPI’s and ultimately optimize your organization warehouse operations.